Industrial Flooring Solutions in Los Angeles, CA
Industrial flooring is a critical investment for businesses requiring durable, long-lasting surfaces that can withstand heavy machinery, foot traffic, and various operational demands. At Los Angeles Flooring Company, we specialize in creating customized industrial flooring solutions tailored to meet the specific needs of each facility in the Greater Los Angeles area. Our industrial epoxy flooring systems provide exceptional durability while offering chemical resistance, safety features, and aesthetic options that enhance your workspace.
We understand that different industries have unique flooring requirements. Manufacturing plants need floors that can withstand heavy equipment, warehouses require surfaces that minimize dust and facilitate smooth logistics operations, and food processing facilities demand hygienic, easy-to-clean surfaces. Our team brings years of experience in designing and installing industrial flooring solutions across Southern California.
When you partner with Los Angeles Flooring Company, you gain access to our comprehensive consultation process where we assess your facility's specific needs and recommend the optimal flooring system. We pride ourselves on using premium materials and employing skilled installation technicians who follow industry best practices. Feel free to contact us to discuss how we can transform your industrial space with flooring that performs as good as it looks.
Our Industrial Flooring Process
We implement a comprehensive approach to industrial flooring that ensures durability, safety, and performance. Our process addresses structural integrity at every stage while delivering solutions tailored to your specific industrial environment.
Visible Cracks and Chips
We begin with a thorough site evaluation to understand your facility's specific requirements. Our technicians measure the space and analyze traffic patterns, load requirements, and exposure to chemicals or moisture.
We identify existing issues such as floor squeaks, damaged joists, or structural weaknesses that could compromise your new flooring. This detailed assessment allows us to recommend the most appropriate industrial flooring solution for your needs.
Environmental considerations like temperature fluctuations and humidity levels are factored into our recommendations. We also discuss your maintenance capabilities and aesthetic preferences during this stage.
A comprehensive written assessment is provided, detailing our findings and recommendations with transparent pricing options.
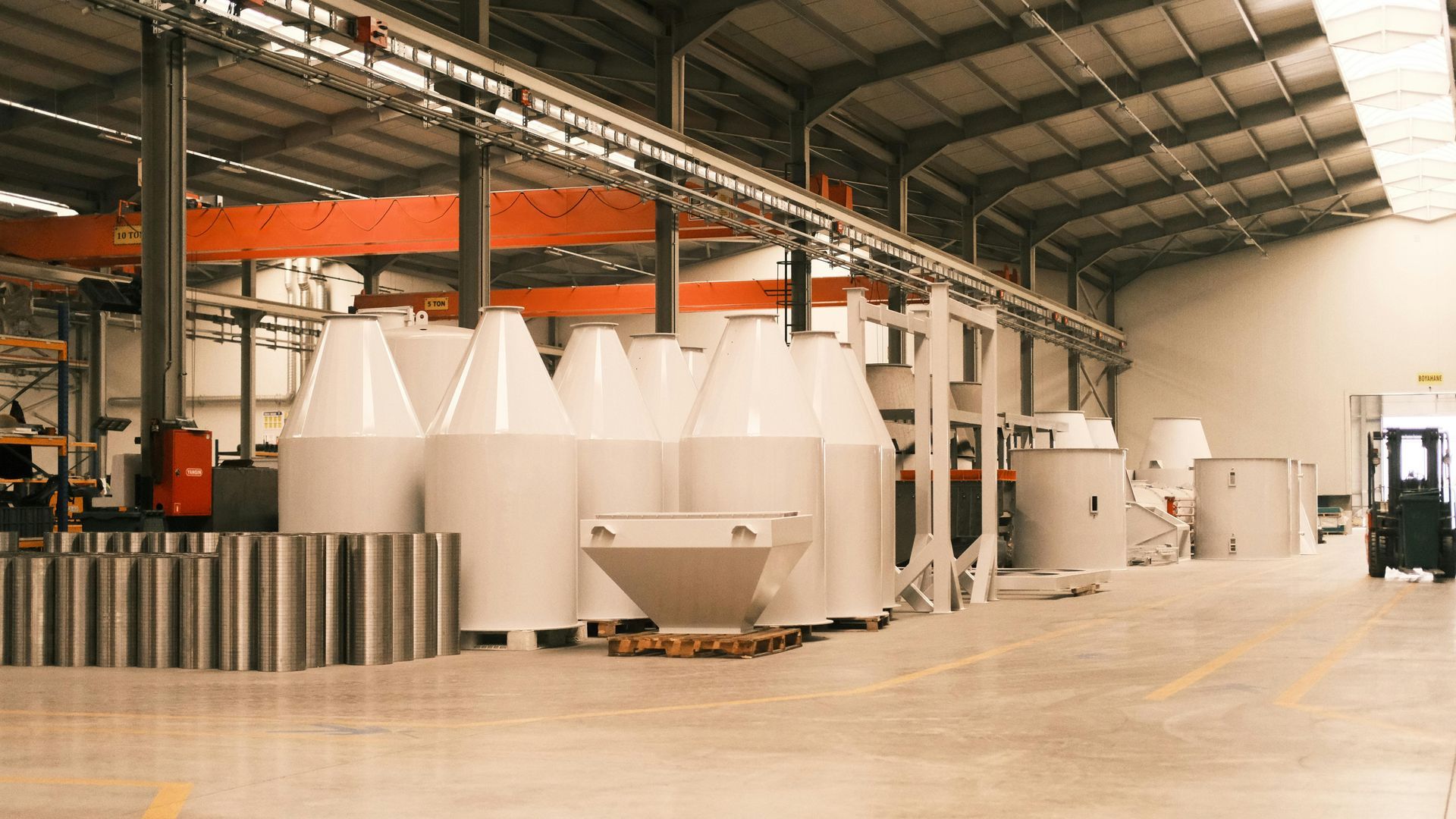
Preparation
Proper preparation forms the foundation of durable industrial flooring. We begin by removing existing flooring materials and thoroughly cleaning the substrate to ensure maximum adhesion.
Any structural issues with joists or subfloors are addressed before proceeding. Concrete floors may require grinding, shot blasting, or patching to create an ideal surface profile.
Our underlayment selection is based on your specific needs. We install moisture barriers where necessary to prevent future damage and extend floor lifespan.
For uneven surfaces, we apply self-leveling compounds to create a perfectly flat base. This attention to underlayment details prevents floor squeaks and premature wear.
We test moisture levels and pH balance of concrete substrates to ensure compatibility with the selected flooring system.
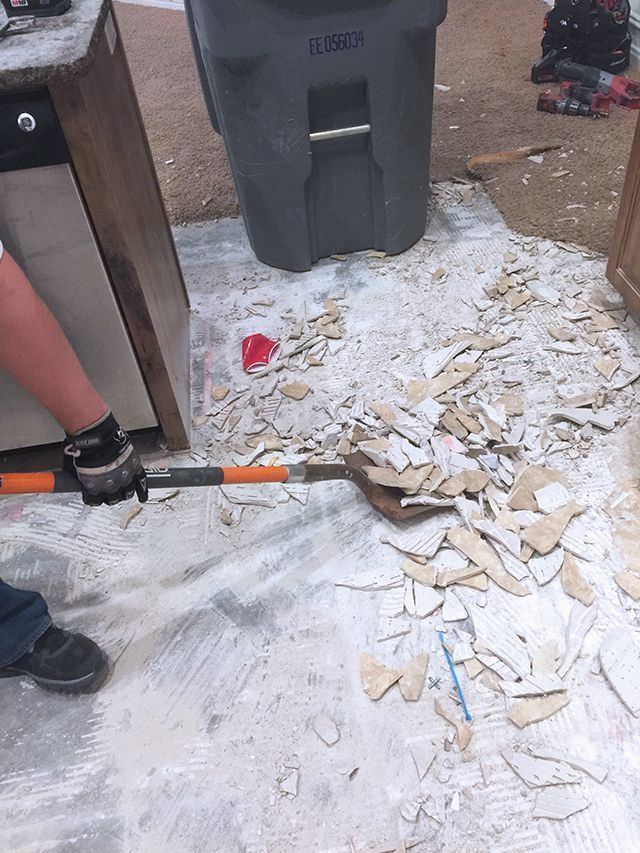
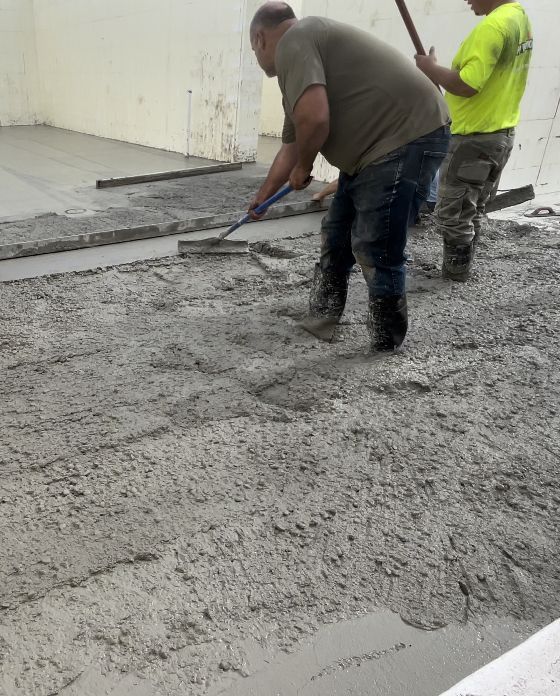
Installation and Finishing
Our installation team uses industry-best practices to apply your chosen industrial flooring system. Whether installing epoxy, polished concrete, or specialized industrial tiles, we maintain precise standards throughout the process.
We carefully monitor curing times and environmental conditions to ensure optimal adhesion and finish quality. Our multi-layer applications provide enhanced durability and resistance to chemicals, impacts, and heavy loads.
Expansion joints are properly maintained or created to accommodate building movement and protect structural integrity. For seamless systems, we apply final topcoats that enhance slip resistance and cleanability.
Quality control inspections occur at every stage of installation. We thoroughly test the finished flooring for adhesion, hardness, and performance before handover.
Maintenance and Repairs
Proper maintenance and timely repairs are essential components of maximizing your industrial flooring investment. Our comprehensive care programs address everything from daily cleaning protocols to handling unexpected damage situations.
Routine Maintenance
Regular cleaning is the cornerstone of industrial floor maintenance. We recommend daily sweeping to remove abrasive particles that can scratch and damage surfaces over time. For most industrial floors, weekly deep cleaning with appropriate pH-neutral cleaners will prevent build-up and maintain appearance.
Different flooring materials require specific care approaches. Epoxy floors benefit from microfiber mopping systems, while polished concrete needs specialized diamond pad maintenance. Urethane floors should be cleaned with manufacturer-approved solutions to prevent coating breakdown.
Preventative maintenance schedules should include quarterly inspections of high-traffic areas, seams, and transition points. These inspections can identify small issues before they become major problems. We provide customized maintenance plans based on your specific industrial environment, traffic patterns, and exposure to chemicals or moisture.
Handling Minor Repairs
Minor damage doesn't always necessitate complete floor replacement. Small cracks, chips, and worn areas can often be addressed through section-by-section replacement or spot repairs, saving both time and money.
For epoxy flooring, we use color-matched patching compounds to repair chips and scratches, followed by a new topcoat to ensure seamless blending. Concrete flooring cracks can be filled with specialized epoxy fillers designed to withstand industrial traffic and prevent further deterioration.
Our repair technicians carry specialized equipment to match existing floor textures and finishes. Quick response to minor damage prevents contamination from entering cracks and causing substrate deterioration.
We maintain detailed documentation of all flooring materials used in your facility, ensuring that any repairs match perfectly with your existing surfaces. This approach maintains both functionality and aesthetic continuity across your industrial space.
Solutions for Water Damage
Water intrusion represents one of the most serious threats to industrial flooring integrity. Our water damage response begins with thorough moisture testing using both surface meters and concrete moisture emission testing equipment.
When water damage occurs, we first identify and eliminate the source of moisture before addressing the flooring itself. This might involve working with plumbing specialists or implementing improved drainage solutions around your facility.
For severe water damage, we employ industrial dehumidification systems to fully dry substrates before repairs begin. This prevents trapped moisture from causing adhesive failure or mold growth beneath new flooring materials.
Our repair solutions may include applying moisture mitigation systems beneath new flooring sections or installing water-resistant alternatives in problem areas. We also provide recommendations for improving facility-wide moisture control to prevent future occurrences.
FAQs on Industrial Flooring Solutions
Industrial flooring solutions come with many considerations, from material selection to maintenance protocols. Below are answers to some common questions we receive from our clients when planning their industrial flooring projects.
What types of industrial flooring are best for manufacturing facilities?
Manufacturing facilities benefit most from epoxy flooring, polyurethane concrete, polished concrete, and resinous flooring systems. Epoxy provides excellent durability and chemical resistance. Polyurethane concrete offers superior thermal shock resistance, making it ideal for extreme temperature environments. Polished concrete delivers cost-effectiveness with good durability. Resinous flooring systems provide customizable solutions with antimicrobial properties for specialized manufacturing needs.
What industrial flooring options are chemical-resistant?
The most chemical-resistant industrial flooring options include novolac epoxy (resistant to harsh acids, solvents, and caustics), polyurethane concrete (excellent against organic acids, alkalis, and thermal shock), vinyl ester systems (superior resistance to extremely corrosive chemicals), and specialized chemical-resistant epoxies. These systems create impermeable barriers that prevent chemical infiltration and substrate deterioration even in highly aggressive environments.
How much does industrial flooring cost per square foot in Los Angeles?
In Los Angeles, industrial flooring costs typically range from $3-$12 per square foot. Basic epoxy systems start at $3-$5 per square foot, while mid-range polyurethane and specialized epoxy systems cost $5-$8 per square foot. Premium systems with customized features, including chemical resistance, antimicrobial properties, or decorative elements, range from $8-$12+ per square foot. Pricing factors include substrate preparation requirements, system complexity, and project size.
How long does industrial flooring installation take for a 10,000 sq ft warehouse?
Industrial flooring installation for a 10,000 sq ft warehouse typically takes 5-10 days. This includes 1-2 days for surface preparation, 1-3 days for repairs and priming, 1-2 days for base coat application, 1-2 days for topcoat application, and 1-2 days for curing before full-weight traffic is permitted. Timeline varies based on system complexity, substrate condition, and environmental factors.
Can industrial flooring be installed while operations continue?
Yes, industrial flooring can be installed while operations continue using phased installation approaches. This involves sectioning the facility and completing one area at a time while maintaining production in others. Weekend or off-hours installation is also common. Mobile barriers and temporary ventilation systems help contain dust and fumes. However, partial operations during installation may extend the overall project timeline by 20-30% compared to full facility shutdown.